LHC Conference 2023: Let's Build a Better Tomorrow
The LHC London and South East conference at the Hilton Hotel in Dartford, on June 13 continued to demonstrate the need for innovative solutions and opportunities to build sustainable, cost-effective, and high-quality homes for the UK’s social landlords.
From tackling challenges brought by traditional construction practices, which are often time-consuming, resource-intensive, and financially burdensome; to finding ways to reduce the carbon footprint of our built environment, the conference brought together several of our clients, partners, and team members, from London and Southeast region, to discuss the limitless possibilities of innovation.
It was also a special day for us as we launched our brand-new Modern Methods of Construction New Homes (NH3) framework.
If you missed attending the conference, then do look at the summary of the discussion points below -
What Experts Said: MMC Vs Traditional
Launching the NH3 framework and stressing the importance of modern methods of construction, Jennifer Castle, COO at LHC, and the chair of the event said, “The shortage of affordable, high-quality housing has reached alarming levels, and as social landlords, and those serving the public sector we are under increasing pressure to find innovative solutions. Fortunately, we have at our disposal a powerful tool that can help address this crisis head-on: modern methods of construction.”
She further added, “Traditional construction practices simply cannot keep pace with the growing demands of our population. By embracing innovation, we can revolutionise how we build homes and create a sustainable, cost-effective, and high-quality housing solution.”
In conversation with our Chair, Jennifer Castle, were some of the brilliant delegates: One of them being Syreeta Robinson-Gayle, Head of Affordable Housing, Barratt London. When asked if adopting modern methods of construction (MMC) is a viable solution for addressing the pressing issue of affordable housing, considering the increasing pressure on social landlords to build homes to meet housing demands and combat homelessness, she replied, “ From the perspective of offsite manufacturing there’s still a piece of work that needs to be done. Too many people still link it to post-war prefabricated houses and come with negative connotations. Those that see the past often consider them to be difficult to maintain, which simply isn’t the case. At Barratt, we continue to build houses using Cat 1 manufacturing and demonstrate the benefits of doing so to those that live in them”
Whilst Category 1 Volumetric buildings are still a new and different concept to adjust to, at the panel all agreed that those who have been working in the construction industry for a long time have encountered some element of off-site. The seven categories as outlined here demonstrate that it is likely that all buildings have an element of offsite, whether it be full modules or roof trusses. The LHC framework offers a solution for all approaches from full turnkey volumetric to hybrid traditional and offsite solutions.
When asked about the advantages of MMC over traditional home building, Dan Macpherson, Executive Director, Henry Riley argued - “Every construction project must have traditional elements as well for us to incorporate MMC in our future building projects. They must go hand-in-hand together.”
Dean Fazackerley, Head of Technical Procurement, at LHC, further added, “MMC helps the industry-wide drive to reducing embodied carbon and achieving net zero but some perceptions of what can be achieved through MMC need to change. Working alongside traditional build approaches MMC can deliver innovative design, efficient, cost-effective, and exciting buildings for our clients and communities. By blending innovative technologies and existing techniques MMC can also bring new skills and employment opportunities for individuals wherever they are in their career.”
Well, in the world of bricklaying robots and 3D printing, the significance of smarter construction methods and robotic technology cannot be denied either. To this, Nick Beard, Technical Officer at LHC, added “Artificial intelligence is now becoming more sophisticated and commonplace across all sectors, including construction. It is essential that our industry embraces the use of AI as a modern, and cutting-edge technology to help drive innovation in the way we design and deliver buildings.”
Environmental concerns are at the forefront of our collective consciousness, and we are responsible for reducing the carbon footprint of our built environment. “Modern methods of construction provide us with an opportunity to adopt greener practices. From using eco-friendly materials to integrating energy-efficient systems, we can design and construct homes that minimise their impact on the environment. By prioritising sustainability, we ensure a better future for our planet while meeting the housing needs of our society,” further added Jennifer.
There was also a lot of conversation about building in factories bringing more than just homes to our land. With an ageing workforce, the construction industry needs to find ways to attract and retain skilled workers. Ryan Geldard, Director at M-AR offsite described the success they have had in introducing more flexible work patterns and more comfortable working conditions without the need to be on-site early in the morning. By doing so, more people can work for longer and to a schedule that supports their personal circumstances.
Syreeta also commented on the need to increase representation, discussing the all too familiar gender imbalance that continues to plague the industry with women taking roles only specific to design, engineering, or administrative positions For the industry to progress she emphasised the need for prioritising diversity and inclusion, and to work towards a sustainable business model that continues to attract new and retain fresh talent. It is imperative for clients to commit to visible pipelines to give confidence to those seeking to join the industry that there is a future available for them.
Nick Beard made a brilliant analogy between social media and MMC, “The innovative appeal of MMC will soon encourage young people to be the pioneers of construction, and we’re at the precipice of it taking off. Watch this space!”
Sums up Brian George, Senior Project Manager Fire Safety at MHS Homes Group, “I thought that the panel was well picked and all had positive comments to offer, which I must say helped many understand MMC better.”
Watch our exclusive showreel on the event, here!
The LHC Approach
LHC has been at the forefront of MMC, introducing the first Offsite Construction of New Homes framework to the market in 2015, having built over 6000 homes using MMC and June 13th marked the launch of our latest iteration fondly referred to as NH3. The key priorities driving our clients and this product are:
- Encouragement of early collaboration between clients and suppliers to push for aggregation of demand
- Best use of building sustainable and successful projects with PCSAs
- Delivery of Net Zero to meet Future Homes Standards
- Meet high levels of Pre-Manufactured Value
- Provide flexibility for clients to deliver MMC projects how they need
- High quality, more experienced turnkey solutions.
If you would like to learn more about NH3, then do visit our website here. Alternatively, please do not hesitate to contact one of our team members here.
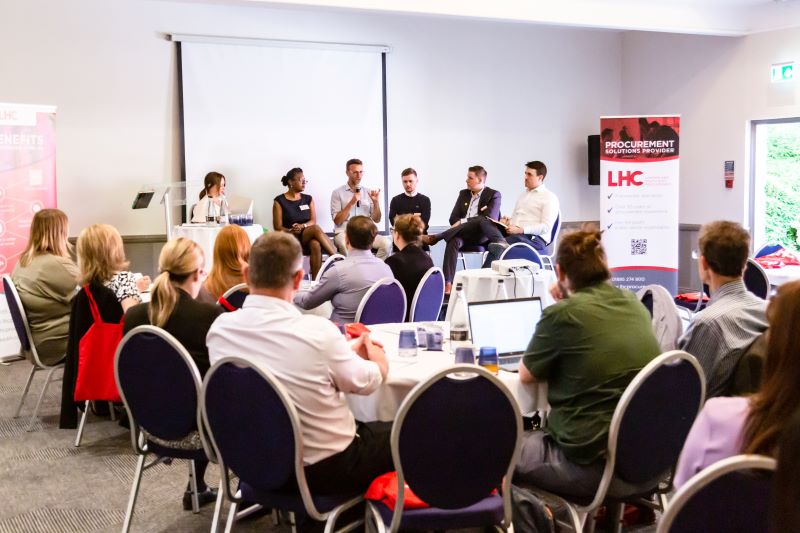