Unlocking the value of MMC for social housing
Tony Woods, Technical Manager at LHC, explains how sector collaboration can help social housing providers to fully embrace MMC
With the many challenges and pressures facing the housing market today – and in particular those faced by the social housing sector – it’s time for providers to start exploring new solutions.
Take up of Modern Methods of Construction (MMC) is slower for the social sector than amongst private companies, but mounting and almost overwhelming issues demand that all possible avenues are investigated.
That means now is the time for social housing providers to start introducing MMC into their programmes.
Demand for MMC is growing
The Government is clearly recognising the benefits of MMC in its quest to deliver 300,000 new homes a year. In Spring 2021 the Ministry for Housing, Communities and Local Government (MHCLG) set up its MMC Task Force, with £10million of seed funding, to accelerate the adoption of MMC across the sector.
At LHC, we’re also seeing demand driven directly by local authorities and other registered providers. Our North and Central England local hub CPC has recently helped both Sheffield and Middlesbrough councils deliver domestic and non-domestic MMC projects respectively. The project in Sheffield saw residents move into their new homes less than five months after the building modules were lifted into place.
MMC can deliver net zero homes more efficiently
Housing providers are under increasing pressure to build more homes, even faster. Offsite factories can turn units around in a fraction of the time of traditional building methods.
In addition, the quality-controlled factory process means MMC builds are super airtight and energy efficient, which also means residents will be far less likely to fall into fuel poverty, and lifetime costs will be lower as less, if any, energy efficiency retrofitting will be needed. MMC also reduces embodied carbon, due to factors including efficient construction, less time onsite, less labour and less transport; this is something that’s going to become increasingly important as the operational carbon from our homes is reduced.
Moreover, as we see economies of scale developing in the MMC market, the costs compared to traditional builds will reduce further and further. However, we at LHC recognise this is probably the biggest barrier to those thinking about entering the market: Currently, the cost of running an MMC project is seen as being too high.
This, in part, is a myth. MMC homes have lower overall lifetime costs, as project delivery is much faster so the sale or rent revenue starts to come in much more quickly. In addition, they also have reduced maintenance costs thanks to the quality-controlled factory environments. But still, the initial project costs can still be somewhat off-putting for many housing providers.
MMC cluster groups drive economies of scale
With this in mind, LHC teams across the country are now working with clients – both housing associations and local authorities – to develop MMC cluster groups to unlock the value in project aggregation.
By bringing housing providers together and combining projects, MMC producers can start to standardise their production processes, bringing costs down. Larger orders also mean we can start to build confidence in the supply chain, leading to further investment in jobs, skills, capacity and technology, again bringing further cost benefits in the future.
Learning from others’ experience
However, any exploration of MMC must be done with expert guidance and support, as there are pitfalls to be avoided.
Again, this is something LHC is looking to provide through our cluster groups. Once projects are identified and providers are happy to work together, suppliers can then be brought on at a very early stage to advise on courses of action. In some cases, we also introduce organisations that are already early adopters, so they can share their own experiences and advise where necessary.
Through our Offsite Construction of New Homes (NH2) framework, we already have the foundation for collaborative working at our disposal. It allows relationships between clients and suppliers to develop and flourish over a longer-term period (from the very early stages onwards) and sets out an integrated supply chain without any legal problems for procurement teams. Early engagement between suppliers and clients through the framework will also ensure the risk load is shared more widely.
Benefiting from procurement frameworks
There is also some concern that MMC housing schemes are too complex to manage, with more stakeholders and more technical areas to keep on top of.
However, through framework agreements, contracting authorities are able to manage the process much more easily through a single point of contact and with the aid of technical expertise across all RIBA Plan of Work 2020 stages.
Our Offsite Project Integrator (OPI1), framework provides technical support at every stage, making available specialist consultants to help make the business case for MMC housing.
Early adopters reap the rewards of MMC
Many local authorities are now starting to look past these barriers to entry and realising the value MMC provides; in fact, our MMC framework has already led to a pipeline of nearly 7,500 MMC homes across 150 projects. I expect to see this number increase ever further, not just because of the Government’s ever-growing preference for MMC, but also because housing providers are seeing all of the benefits that MMC brings.
But, it should also be recognised that over-stretched local authorities need proper resourcing, and technical and practical guidance, as well as help to recognise where the value for money is to be found. This is where LHC’s experience, local procurement expertise and MMC knowledge can help.
MMC is undoubtedly the future for house building, and local authorities can help to lead the way.
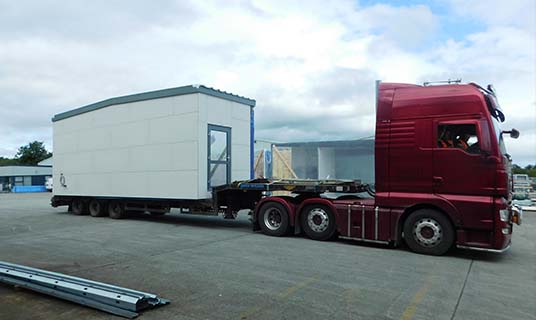